8 millioner grunner til at ansatte styrer produksjonen
Lønnsom involvering og ansvarliggjøring
Toyota overtok på midten av 1980-tallet Fremont bilfabrikk i USA, som var en av General Motors verste, – kjent for sex, alkohol, narkotika og defekte biler.
Under GM’s ledelse av fabrikken, før Toyota kom inn, var det en innprentet hovedregel: Samlebåndet måtte aldri stoppes. Lee, en mellomleder som overvåket anlegget, oppsummerte det slik: «Hvis du så et problem og stoppet produksjonslinjen, fikk du sparken.» Montøren Billy Haggerty så biler med alle typer feil og mangler rulle gjennom på samlebåndet, uten at noen gjorde noe for å korrigere dem. Noen av arbeidstakere hatet ledelsen så mye at de saboterte kjøretøyene de produserte. Cola-flasker ble passert inne i dørpanelene, så de ville skrangle rundt og irritere kundene. Det var biler med motorer montert baklengs, biler uten ratt eller bremser. Feilene ble reparert senere i et verksted utenfor fabrikken, noe som kunne gjøre enda mer skade på kjøretøyene.
Og selv om det ikke er verifisert at motorer faktisk ble plassert bak-frem, så er historien betegnende for holdningen og kulturen ved bedriften. Fabrikken hadde et – sannsynligvis helt fortjent – rykte for dårlig kvalitet, lav arbeidsmoralen, og overdrevent fravær.
Men i et historisk joint venture utviklet Toyota fabrikken til et av GMs beste, praktisk talt over natten, med mange av de samme medarbeiderne, i den nye NUMMI-fabrikken (New United Motor Manufacturing Inc.).
Det originale GM-anlegget stengte i 1982, og skulle gjenåpnes i et samarbeid mellom Toyota og GM. Men både medarbeiderne og fagforeningen UAW var litt overrasket over at Toyota valgte å ansette en stor del av den tidligere arbeidsstokken. De ble fløyet til Japan og fikk lære en helt annen måte å produsere biler på.
Her ble folk delt inn i mindre arbeidsgrupper på bare fire eller fem, og de byttet jobb etter noen timer for å unngå monotonien. En teamleder ville umiddelbart komme og hjelpe til, hvis noe gikk galt.
Toyota tillot blant annet den enkelte medarbeider – uten lederens
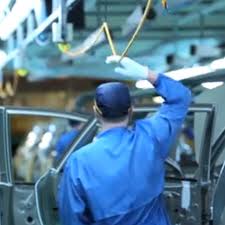
tillatelse – å stoppe produksjonslinjen umiddelbart når han eller hun anså det for å være nødvendig. Toyotas løsning på dette var et tynt nylontau som hang på kroker langs samlebåndet. Det ble kalt Andon-snoren, og når en medarbeider trakk i den, stoppet samlebåndet.
Resultatet av denne involveringen var at Toyota bygget flere biler med høyere kvalitet enn det noensinne var blitt bygget ved Fremont-anlegget. I desember 1984 rullet den første bilen, en Chevy Nova, ut av samlebåndet i NUMMI. Årlig produksjon ved anlegget toppet seg i 2006, med 428.632 biler. Toyotas filosofi om ansvarliggjøring av medarbeiderne gav bilkonsernet et globalt kvalitetsforsprang på 10-15 år i forhold til konkurrentene.
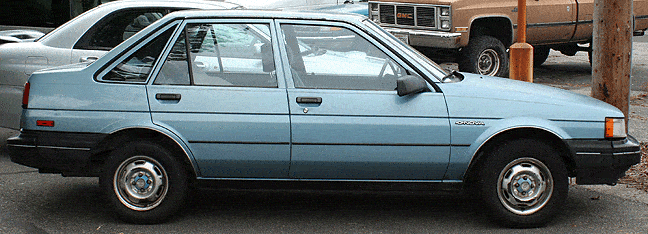
Involvering av medarbeiderne skapte nye og innovative måter å samarbeide på i Fremont-fabrikken. Dette resulterte i en lønnsomhet fabrikken under sin tidligere, mer autoritære, GM- kultur ikke hadde vært i nærheten av.
Eventyret tok dessverre slutt i 2010, som følge av konkursen i General Motors, men da hadde fabrikken, NUMMI (New United Motor Manufacturing Inc.), produsert 8 millioner biler av topp kvalitet.
Men et nytt eventyr lå og ventet: Noen måneder senere, i mai 2010, ble fabrikken overtatt av Tesla, som nå produserer sine biler der.